定期分解整備の勧め、及び機械器具設置というもの
今回は、定期的な分解整備の必要性と、機器の据付方法による耐用性の違いのお話しをさせていただきます。 施工前の外観の状態は比較的きれいです。
ですが、分解してみると内面のナイロンコートの剥がれが目立つ他、機械加工面の腐食が目立ちます。
これらの部分は腐食の程度に応じ、再加工をして組み立てます。
これには構造と動作時の負荷のかかり方の理解が必要です。 ポンプを組立復旧した後はポンプとモータの芯出し調整を行いますが、元々の据付方法が機械器具設置とは異なる簡易的な据付をしていたために、経年劣化により機械ベースが芯出し不能なレベルまで歪んでいました。
そこで、緊急で機械ベースの歪みを修正しました。
修正後、水の浸入防止措置を行います。
こういった補助作業を経て、運転確認までたどり着きました。
軸受の振動値は基準値よりもはるか下の良好な状態でした。
冒頭の極端な腐食は、普段の保守点検及び調整が不適切であったことと、前回整備から今回までの期間が長すぎたために起こったといっても過言ではありません。 適切な期間内に整備を行っていれば、整備を行いながらさらに長期間の機器の使用が可能であったと思われます。
ですが、残念ながらこの機器は次回整備は不可と判断せざるを得ません。
トータルコストの削減の為にも、早めの正しい点検及び整備を推奨いたします。 また、正しい機械器具設置を行うことにより、機器の健全な状態が保てます。
実際にこういった据付では、振動が振動を呼ぶ共振が発生する事が多く見られ、軸受の振動値を計測してもどこがどう悪いのかの正しい判断ができないことが多くなってしまいます。 今回も、機械器具設置業者の知識が十分でなかったために、極度の腐食と機械ベースの変形を起こし、復旧不能になってしまったという事例となりました。 正しい据付・点検・判断・整備・運転確認は機器を健全に保つうえで非常に重要です。
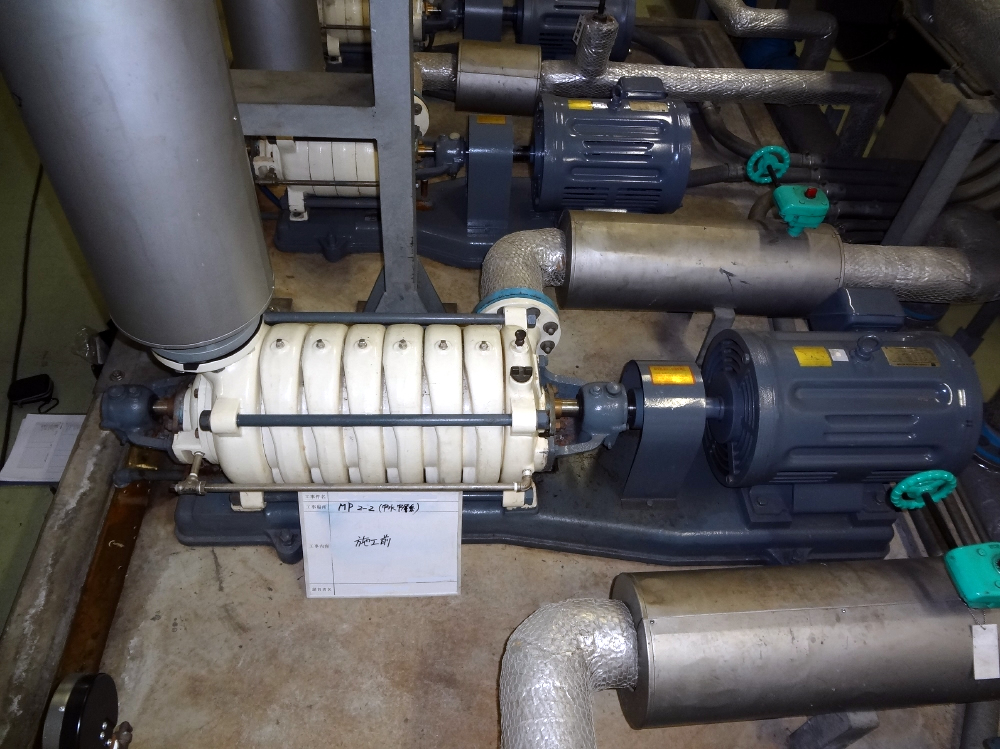
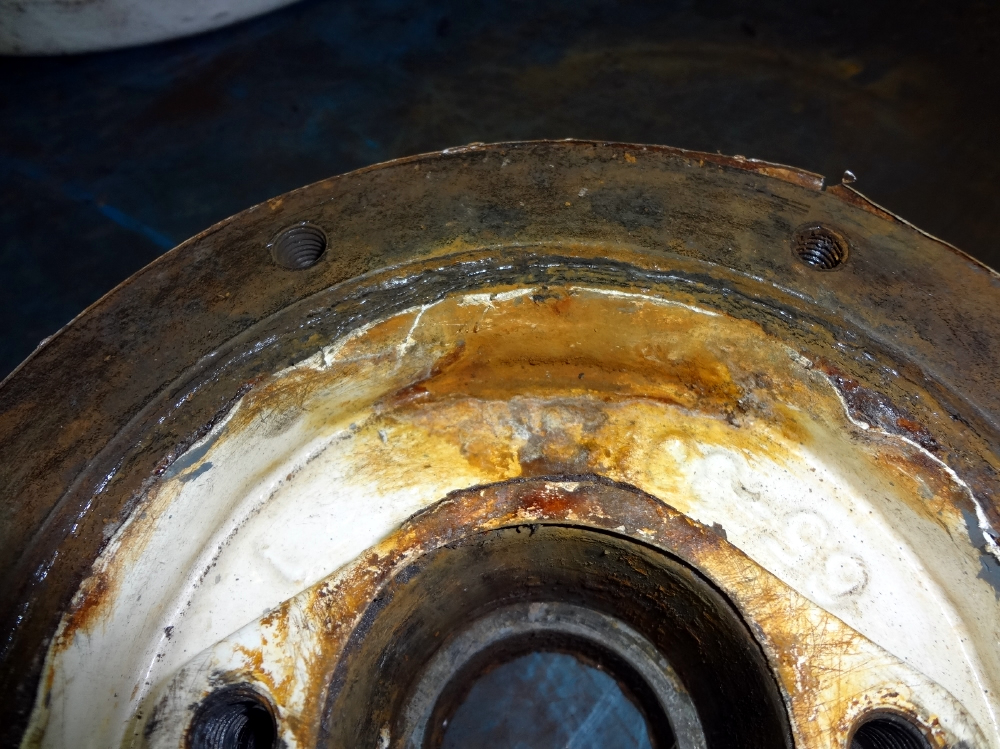
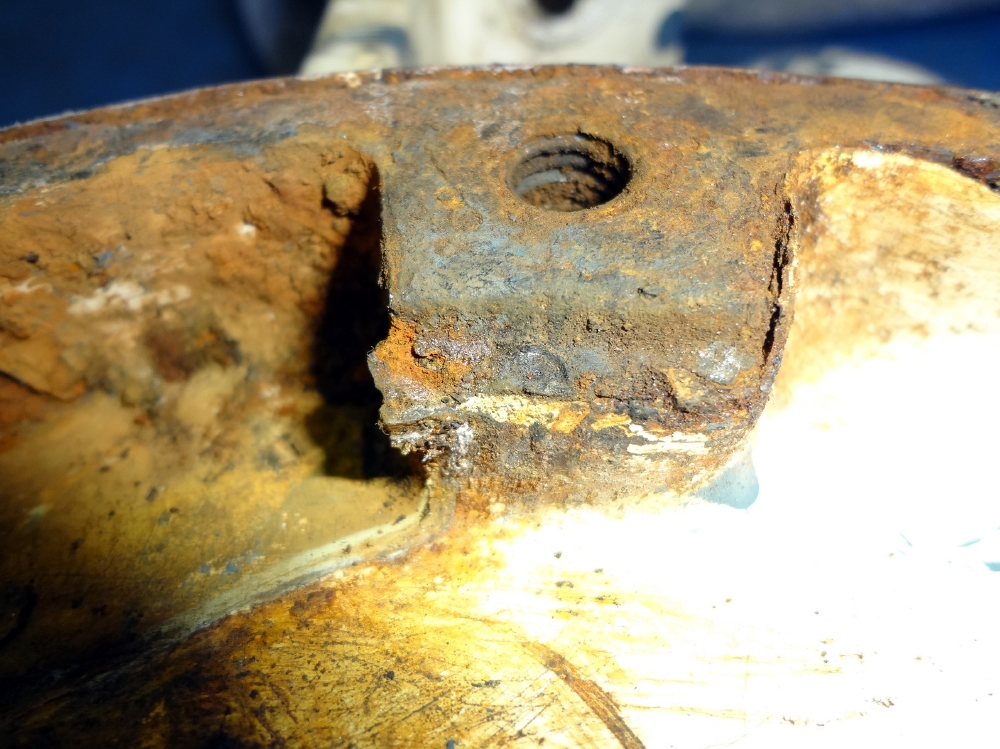
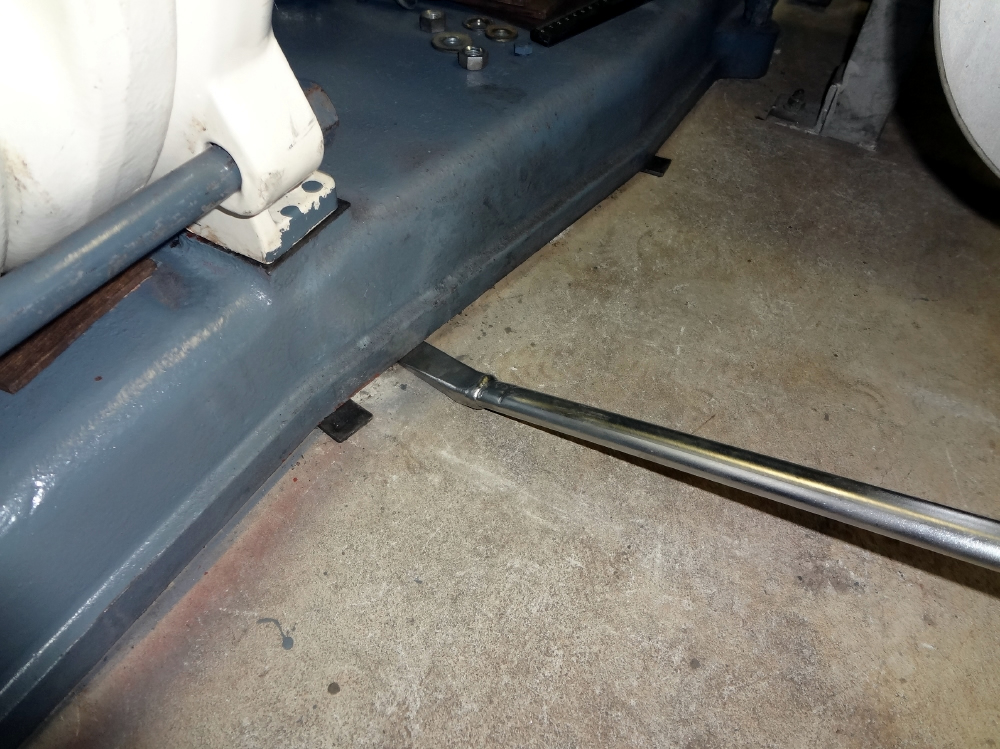
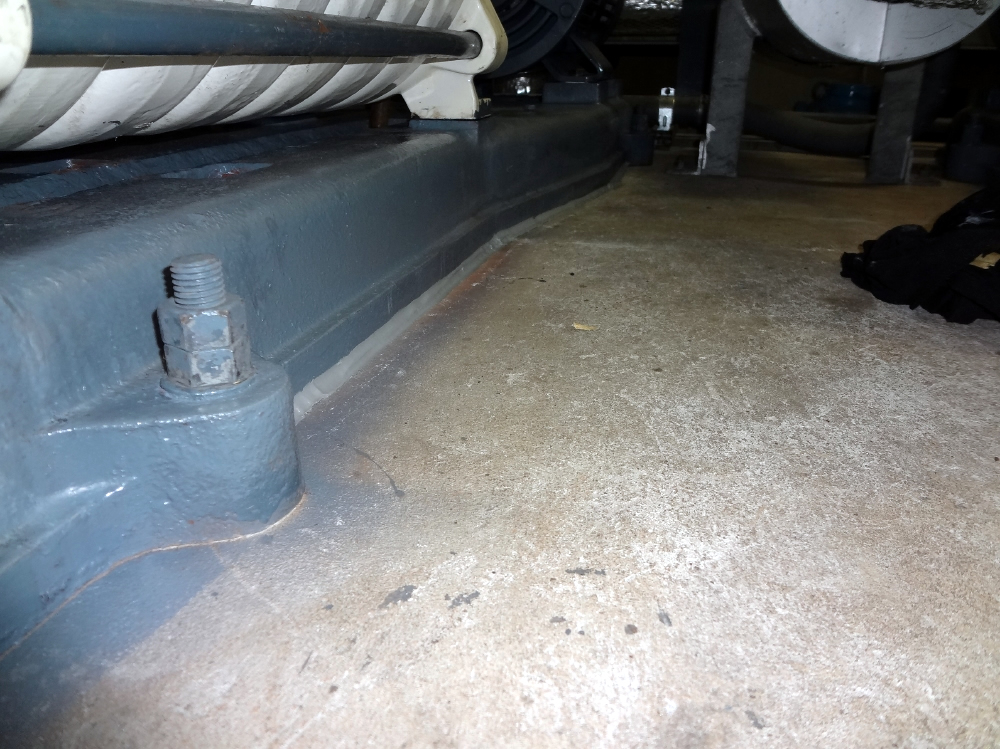
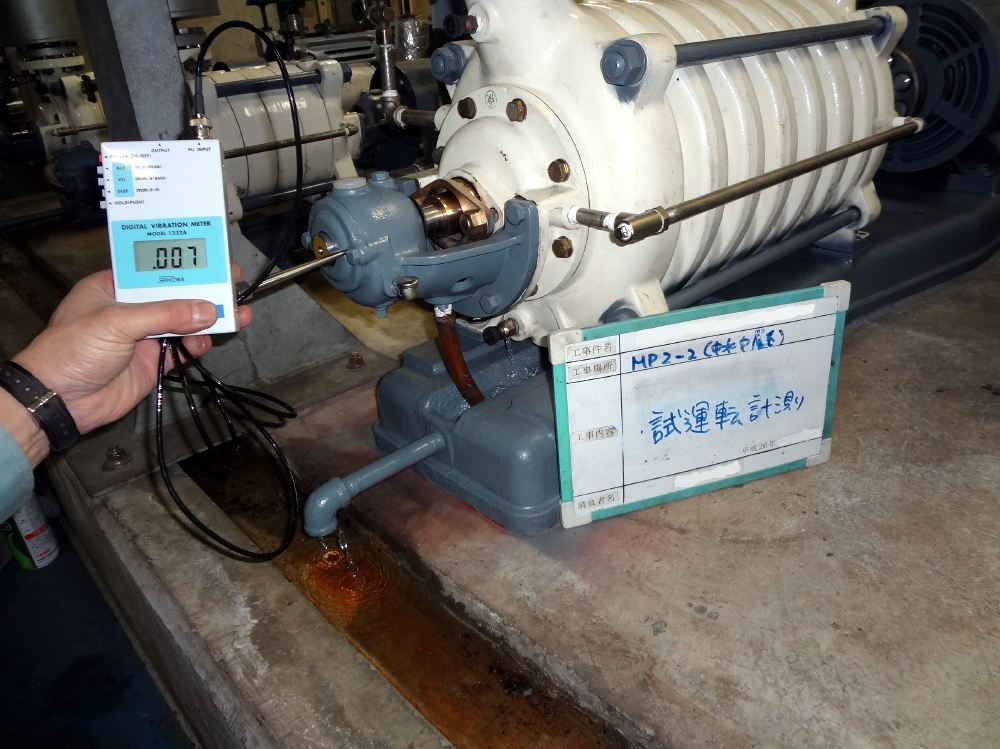